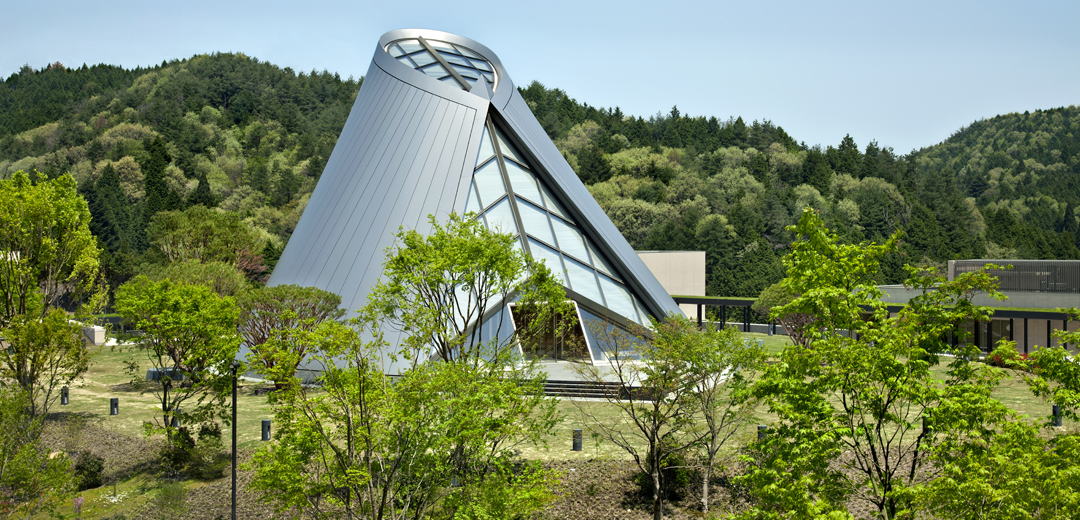
The top quality of material and detail
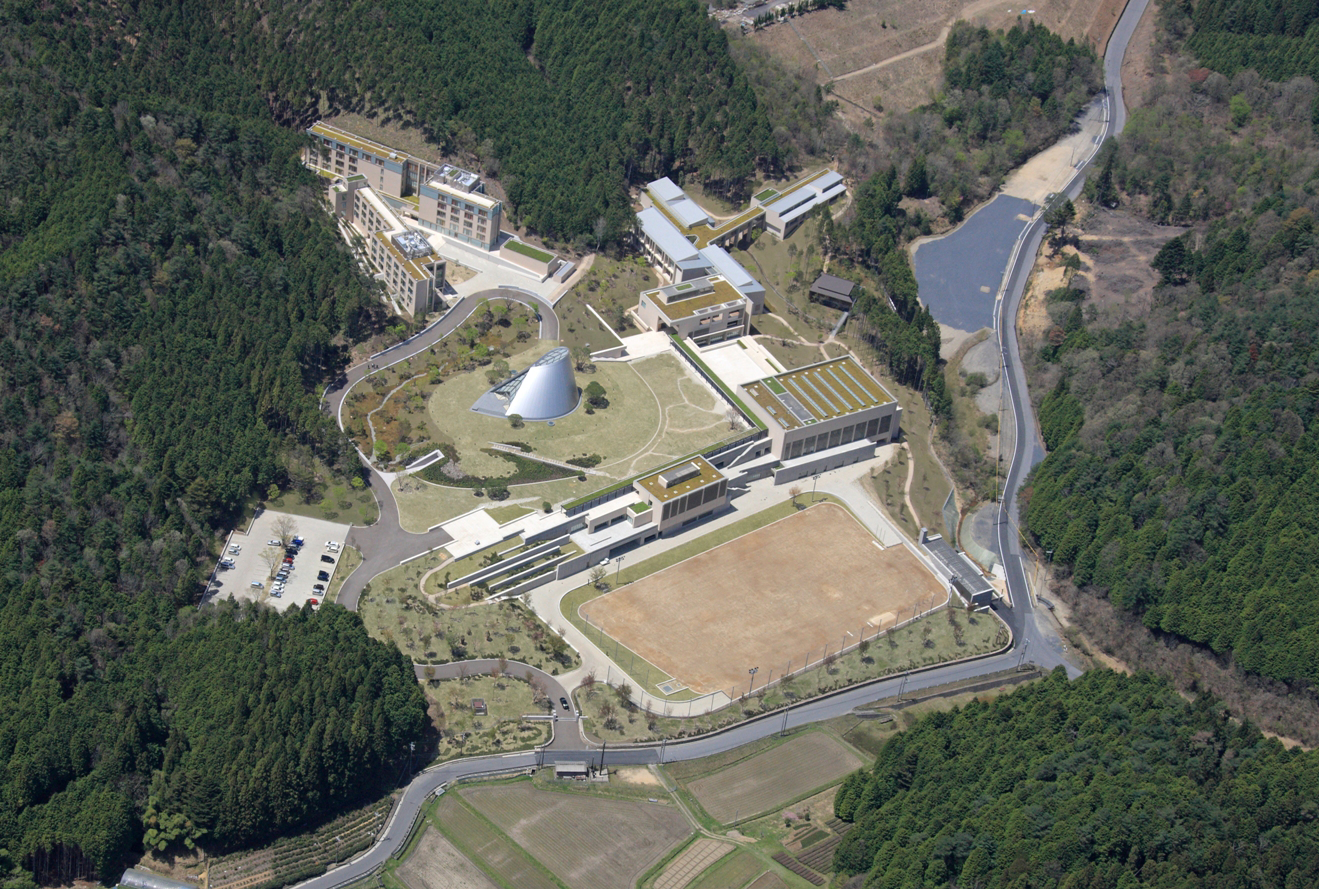
It was the biggest project for me to build a dormitory with a floor space of about 25,000 m² on the site of 8 hectares in Koka city, Shiga Prefecture. As a design director of the Japanese side, it is a huge project for five years including building design and supervision, such as development permission, permission of the Natural park law, school permission acquisition, etc. The number of designers and constructors, the size of the building, and the quality as a high-end architecture are by no means unprecedented.
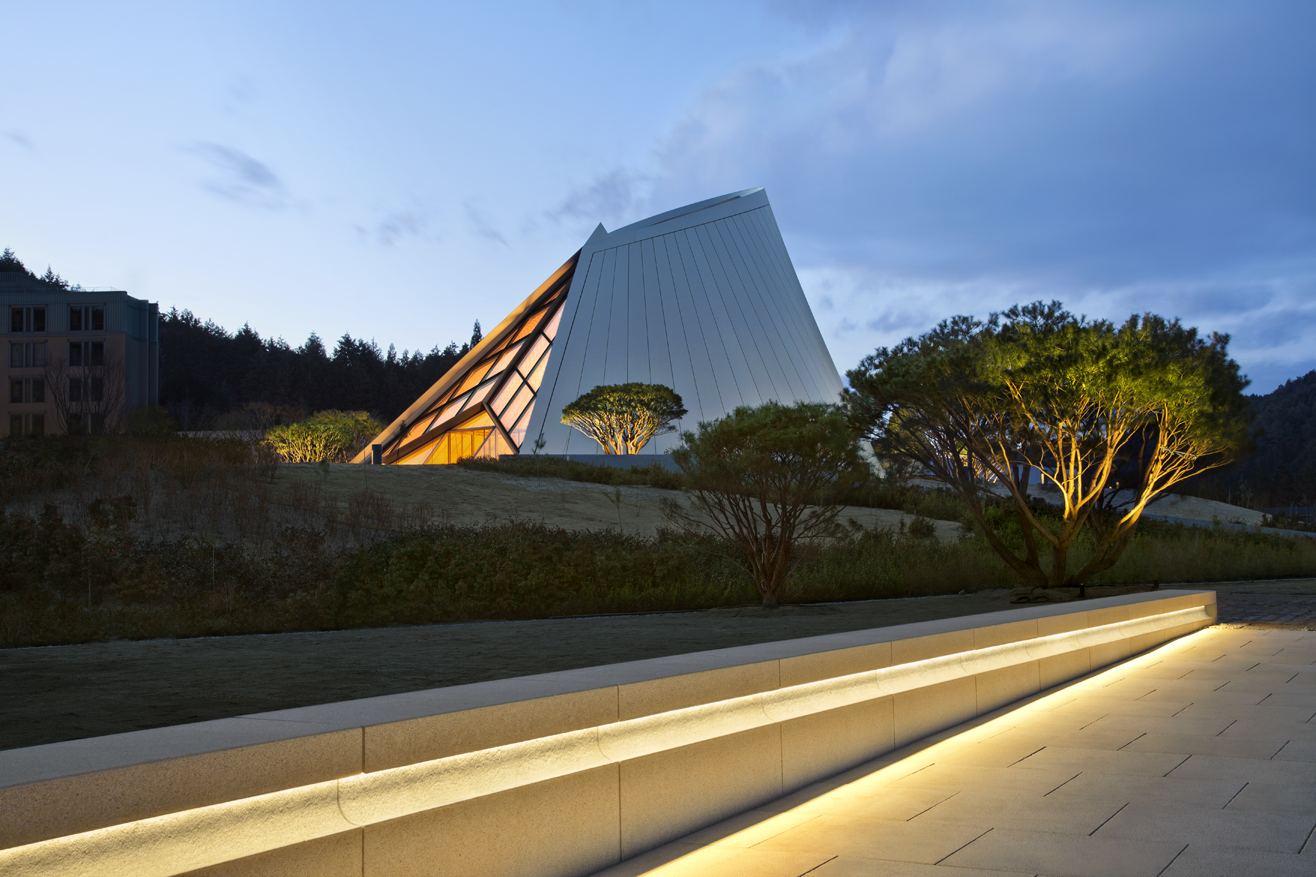
Although it sounds good to say that it is a dynamic process that different kinds of buildings such as Mr. Pei by chapel and io Architects, school buildings, dormitories, tea ceremony room buildings, etc. are in close contact with the NY side while progressing at the same time, The pressure to manage carefully so that none of them are overlooked was one of the largest in the past.
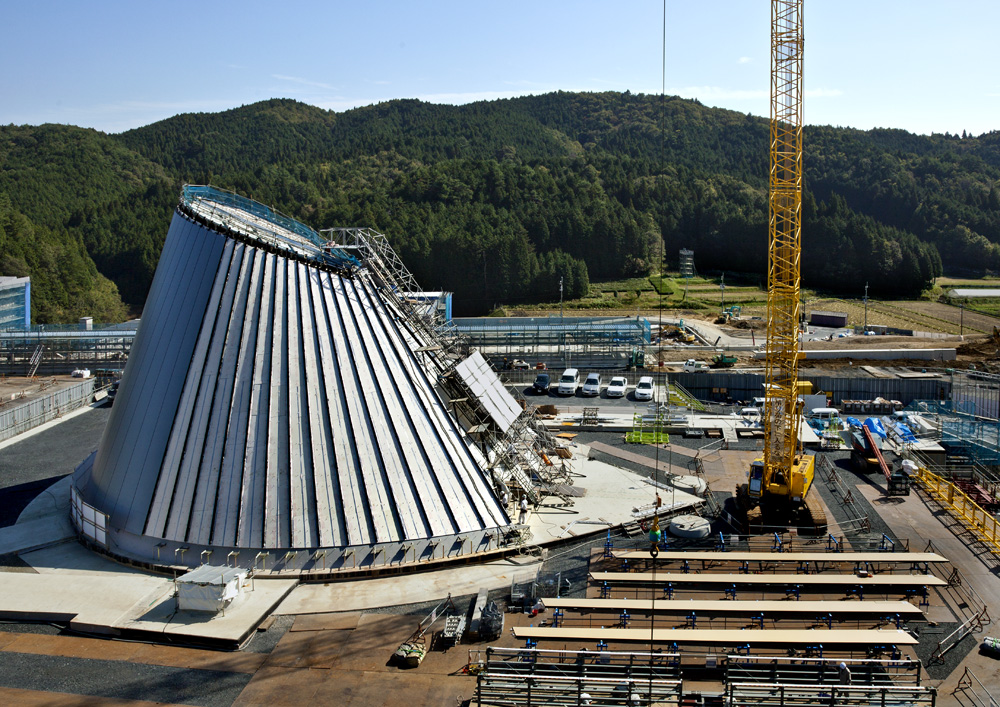
When we say architectural design practice, the design focusing on the creation of the form first appears, but in fact one more important element is the management of the project. A huge building project will involve a number of designers, multiple layers of contractors, various consultants and clients. While grasping the movements of these characters and putting out necessary information, we will grasp the whole picture. It is a necessary management skill irrespective of the scale, but it has been 5 years to have a hard-to-change experience on huge projects.
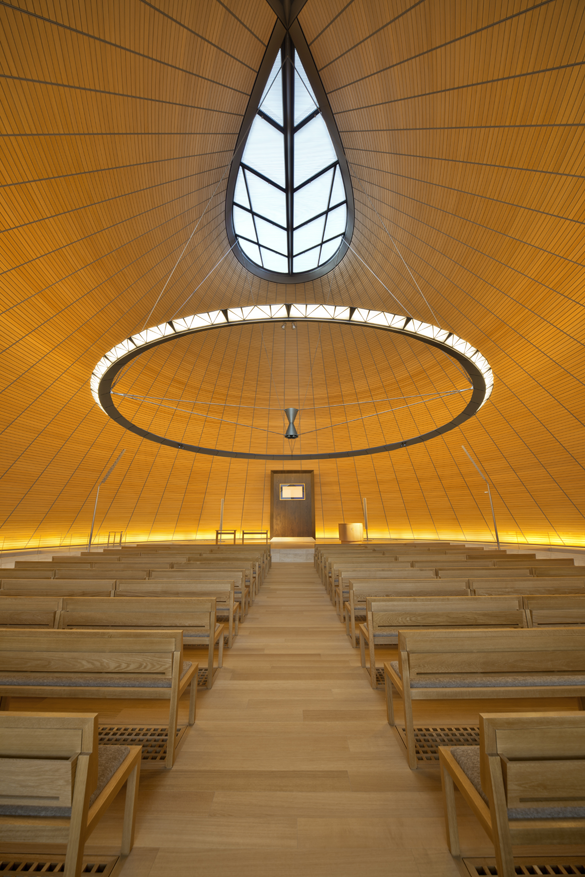
As the Japanese design director, I looked over all of the construction drawings that the building actually plays, as well as the implementation design drawings. I saw the process of building things from the drawing while stamping the number of sheets of inks so that the ink of the seal quickly disappeared. It was such a precious experience. After this project, my confidence that any type of building of any size could be designed and supervised has assuredly developed.
The architect IM Pei who was designing the chapel (born in 1917) positioned this school chapel as “the last project.” As a Japanese, it was an honor to have been chosen as his last project location, celebrating his 90th birthday at the beginning. This is because internationally renowned architects think that building of the highest quality they desire will be made possible only by the highest construction quality in Japan. In the design of this chapel, we decided to create a 3D model at Rhinoceros and share it among designers / builders. It was a very exciting experience to see the 3D model design experts in the general construction company took over our 3d model, regarded it as the official shop drawings, and constructed the chapel directly from the 3d model. It was our new experience which did not go through the conventional shop drawing approval process.
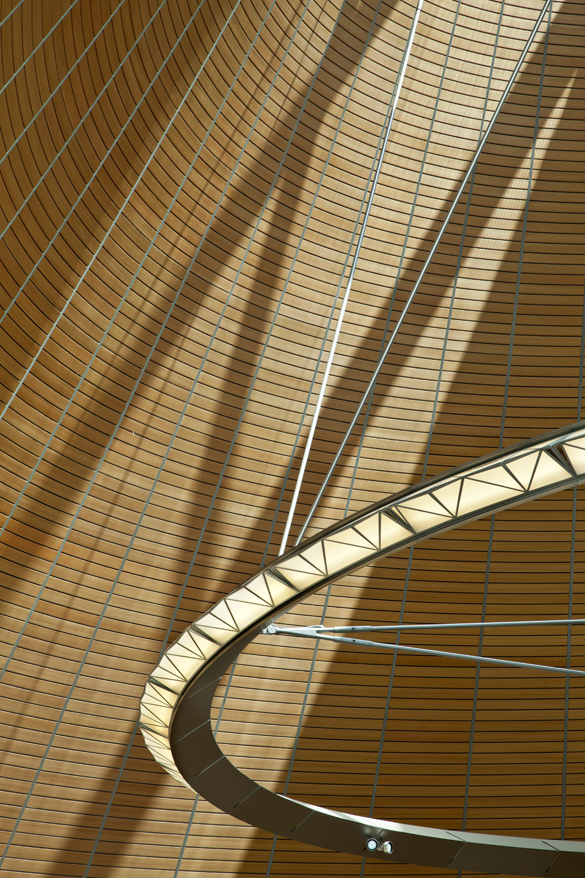
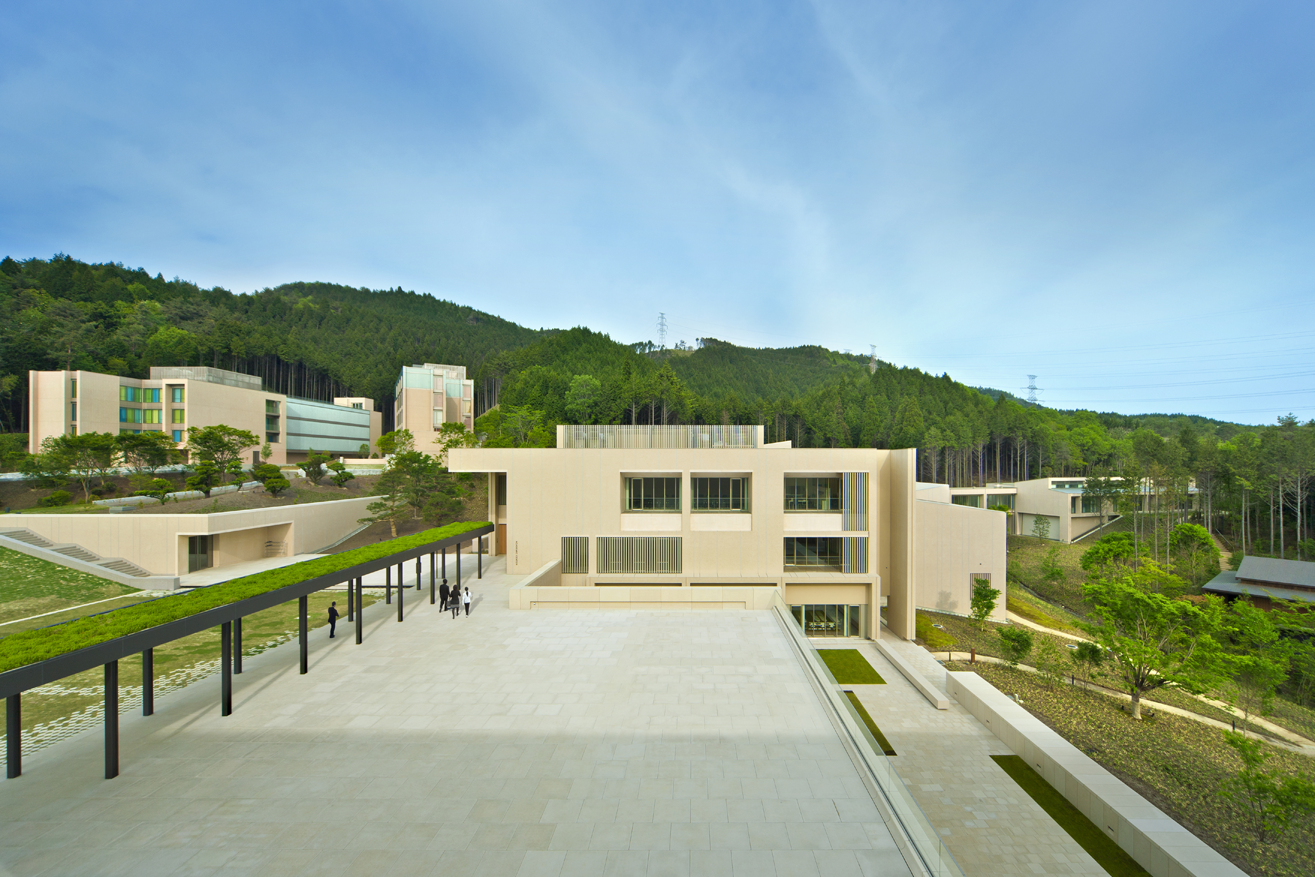
Mr. Pei’s architecture has a way of using distinctive materials. For example, heavily use of beige limestone, Magny, which is the French limestone used in the Louvre museum project. I went to the quarry in the Burgundy region and supervised what kind of quality stone to adopt. Maximum dimensions It is a very valuable experience to know how much you can cut out stone blocks and cut out slabs, that is, you can actually see the most upstream part of the material supply chain. By the way, because we can drink good wine when going to the factory inspection, seniors at Pay ‘s office all seem to have gone to factory inspection.
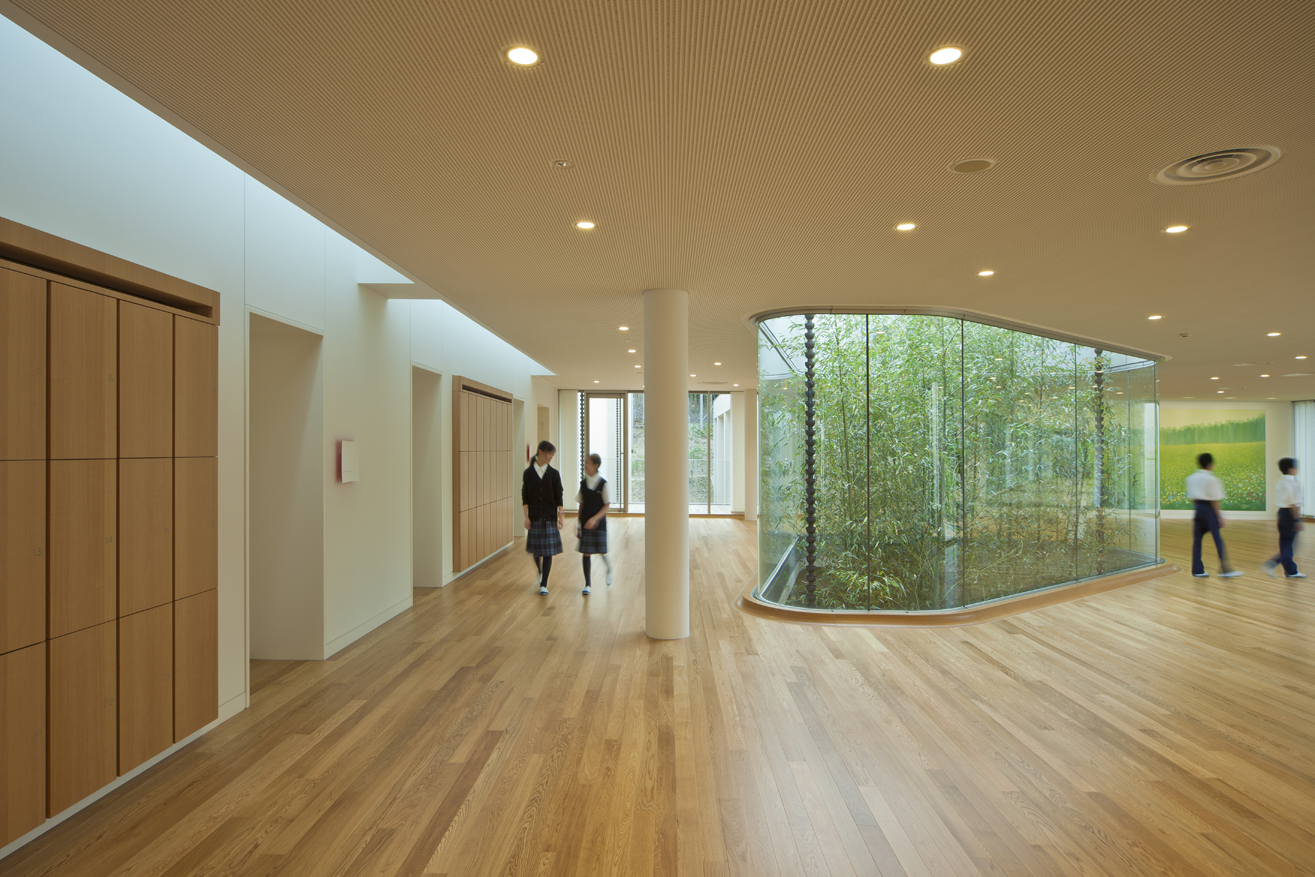
Also, we decided to ask stainless steel exterior materials to Kikukawa Industry in Japan. It is a metal specialized dealer who manufactures the exterior of the Apple store which is deployed all over the world. The exterior material of the chapel has one tertiary surface plate material, approximately 1.2 m in height and 18 m in height. We decided to expand the factory as a result, in order to make this large material special custom surface finish. Kikukawa Industry is responsible for metalworking of various buildings designed by prominent architects from around the world, but it is also encouraging that such a trader is in Japan.
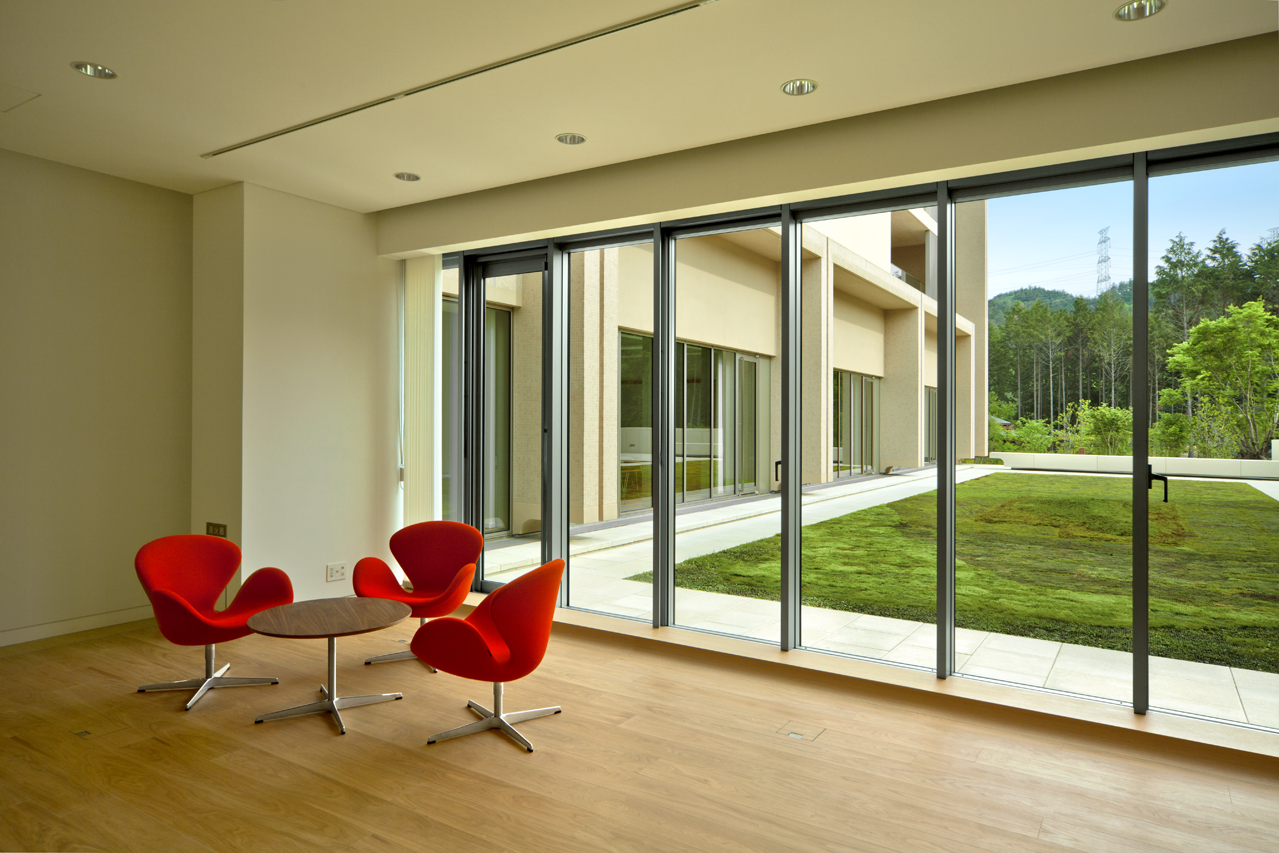
Various consultants’ project participation was also rich in variety. For example, it is also very interesting to see the workings of familiar consultants who have done a number of Pei’s projects, such as structural engineers and lighting consultants from the United States, acoustic consultants from France and so on did. An acoustic consultant who engaged in the acoustic design of music halls by many renowned architects said, “I can see how it will be done in roughly acoustic simulation, but I do not know if I can finally do it, is not it?” Impressive was. I think that a flat communication style that is not formal is a good point of English.
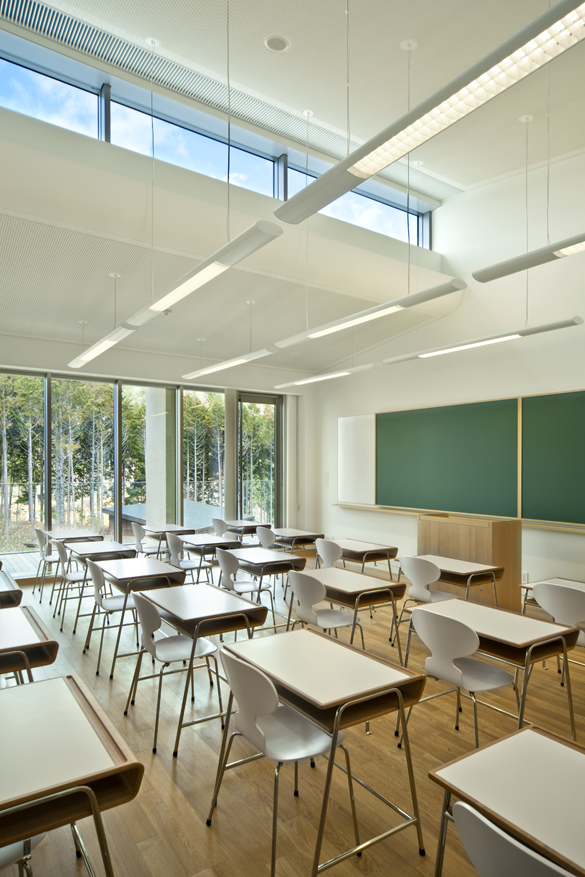
Regarding to the stainless steel, we began by confirming the maximum size available, transformable, and able to construct. There was a challenge how to realize the shape that Pei needs while looking at its limit. And by witnessing the technical strength of the construction side and the unremitting effort to push down the limit, the respect for the constructor has increased. This was the moment when I realized the significance of construction. I was convinced that doing a design that can be constructed ultimately leads to an increase in the quality of the building itself.
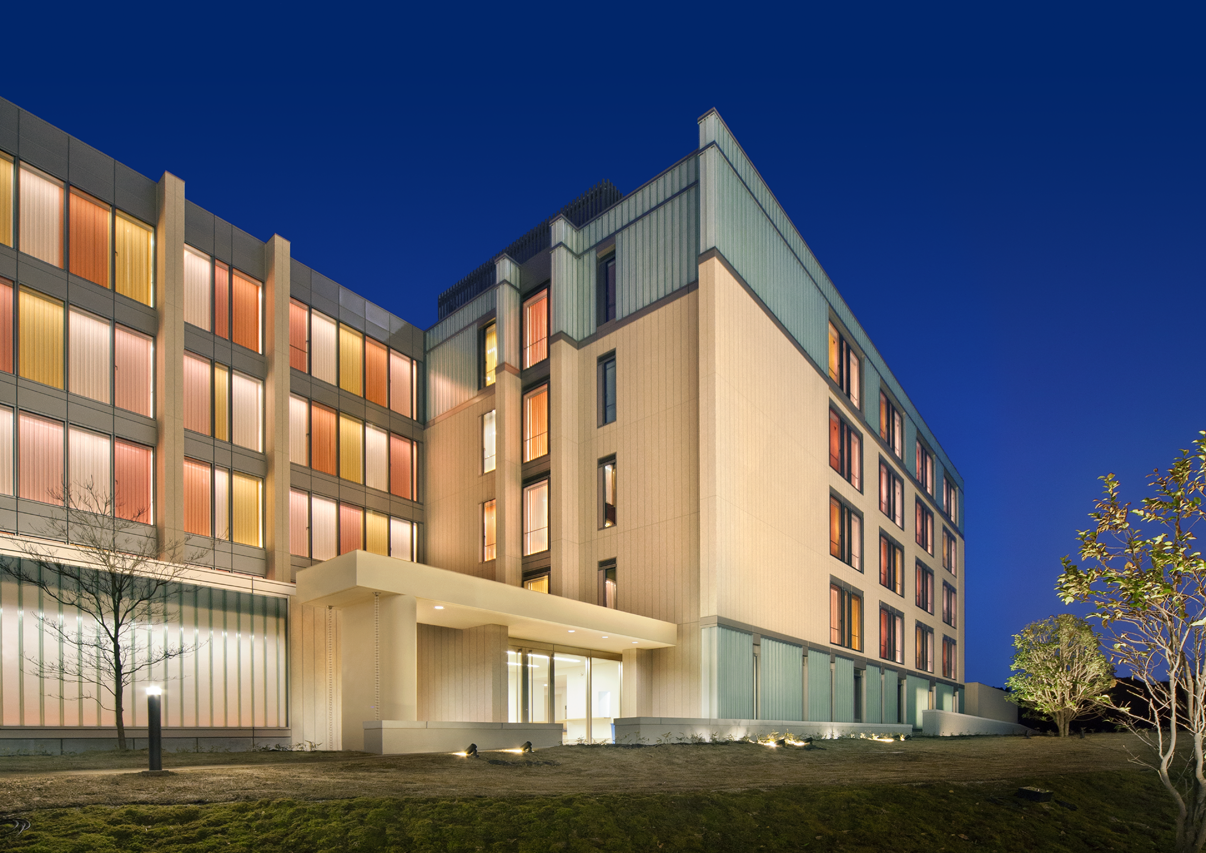
The wood panel used inside the chapel was produced by Kyoto’s Miyazaki timber who also handles the Imperial Palace and the Fukiage Gosho’s furniture, and designed the design designed by the 3D model in Japan It is possible to realize with the handcrafted craftsmanship of Japan, which can only be done in Japan, and the building precision and technology can be said to be constructed.
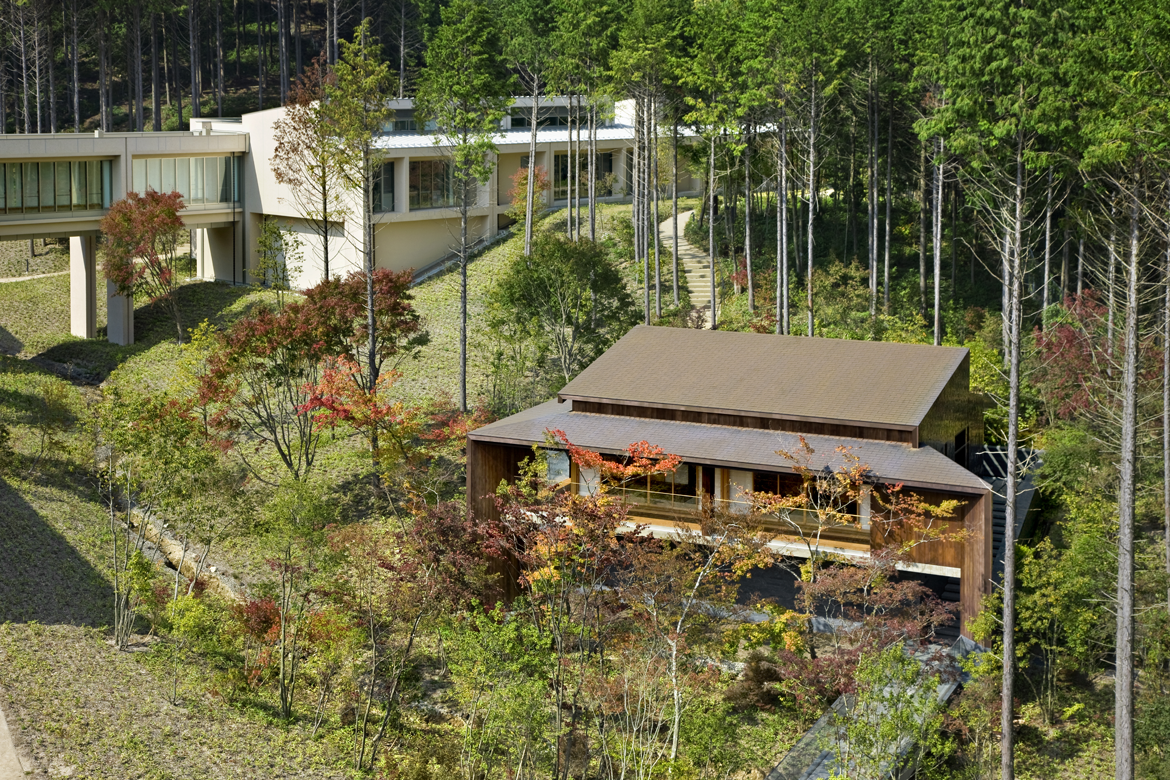
IM Pei’s first project was a chapel. And I put my own architect life as “starting with chapel and ending with chapel”. The rounded shape of the fan shape was decided in a few weeks in a matter of time, but it was surprising since it was confirmed that the intention that decided at the beginning of the project did not blur at all. Moreover, it is not impossible at all in terms of construction and construction, and the fact that it was requested with precision that it is possible to do further stands out his wake up. I never thought that I would be involved in Mr. Pei’s last project since I came back to Japan after having worked at a Pei office since I returned to Japan.